Why Testing of Plastics is Key to Quality Control in Manufacturing
In the modern manufacturing landscape, plastics have become one of the most versatile and widely used materials. From automotive components to consumer electronics and medical devices, plastics play a critical role in product development across numerous industries. However, to ensure that these plastic materials meet the necessary standards of durability, safety, and functionality, comprehensive testing of plastics is essential.
This blog explores why plastic testing is fundamental to quality control in manufacturing and how it helps manufacturers meet performance, regulatory, and safety standards, ensuring consistent product quality.
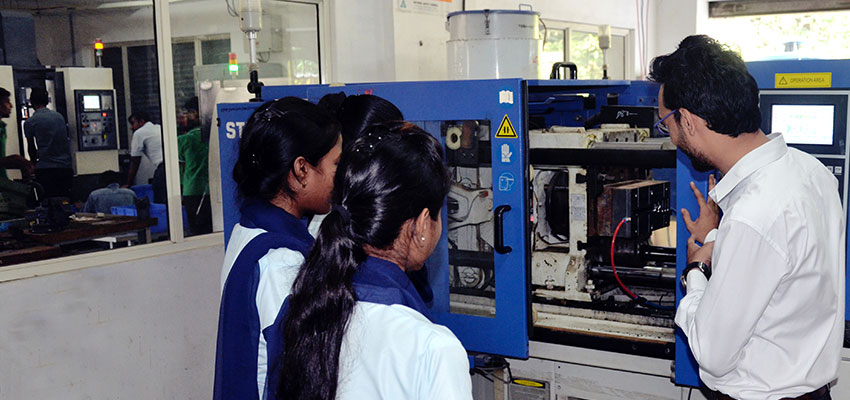
The Role of Plastics in Modern Manufacturing
Plastics offer manufacturers several advantages, including versatility, lightweight properties, cost-efficiency, and durability. Their ability to be molded into various shapes and forms makes them ideal for use in multiple applications, ranging from packaging and automotive parts to medical devices and construction materials.
The Need for Quality Control in Plastics Manufacturing
The sheer variety of plastics, each with distinct properties, means that not all plastics are suitable for every application. Therefore, ensuring the quality and performance of plastic products requires rigorous testing. This process is vital for manufacturers to:
- Prevent product failures or defects
- Ensure compliance with industry and safety standards
- Meet customer and market expectations
- Reduce costs related to recalls, replacements, or legal liabilities
Why Testing of Plastics is Critical for Quality Control
Comprehensive testing of plastics is essential to verify their mechanical properties, thermal resistance, chemical compatibility, and environmental impact. Testing helps manufacturers identify potential weaknesses or issues that could lead to product failure. Below are key reasons why testing plays a crucial role in ensuring the quality of plastic products.
Ensuring Product Performance
Plastics are often exposed to a wide range of environmental conditions, such as temperature changes, mechanical stress, and chemical exposure. Testing evaluates how a plastic material performs under these conditions, ensuring that it will meet the performance criteria for its intended application.
Mechanical Testing: Durability and Strength
Mechanical testing assesses the material's strength, flexibility, and resistance to impact. This is especially important for products that require high performance under physical stress, such as automotive components and industrial equipment. Tests such as tensile testing and impact resistance testing help manufacturers determine whether a plastic can endure the demands of its application.
- Tensile Testing: Measures how a plastic behaves under tension, assessing its strength and elasticity.
- Impact Resistance Testing: Determines a plastic’s ability to absorb energy and resist fracture when subjected to a sudden force.
Compliance with Safety Standards
Manufacturers must ensure that their plastic products comply with safety regulations, which can vary by industry and region. Failing to meet these standards can result in product recalls, legal penalties, and reputational damage. Testing ensures that plastics meet safety regulations, including flammability, chemical resistance, and thermal stability.
Thermal Testing: Heat Resistance and Flammability
Many industries, such as automotive and electronics, require plastics that can withstand high temperatures without degrading or losing structural integrity. Thermal testing evaluates how well plastics can endure heat without melting or deforming. Additionally, flammability testing is essential for materials used in electronics, construction, and transportation to ensure they meet fire safety standards.
- Heat Deflection Temperature (HDT): Determines the temperature at which a plastic deforms under a specified load.
- UL 94 Flammability Testing: Classifies plastics based on their ability to resist ignition and their burning rate.
Enhancing Product Reliability
Consistent product quality is critical for maintaining customer trust and minimizing costly returns or warranty claims. Regular testing during the manufacturing process ensures that every batch of plastic material adheres to the desired specifications, reducing variability in product performance.
Environmental Stress Cracking (ESC) Testing
Plastics exposed to environmental stress, such as temperature fluctuations and chemical exposure, may experience cracking or degradation over time. ESC testing evaluates a material’s resistance to cracking when subjected to both mechanical stress and environmental conditions. This ensures the long-term reliability of products used in challenging environments, such as outdoor furniture, chemical containers, and automotive components.
Supporting Innovation and Sustainability
With increased global attention on sustainability, testing helps manufacturers innovate by developing more environmentally friendly plastics that meet both performance and regulatory requirements. Sustainability testing ensures that new materials are safe, durable, and compliant with environmental standards.
Biodegradability and Recyclability Testing
To meet sustainability goals, manufacturers are increasingly turning to biodegradable and recyclable plastics. Biodegradability testing determines how long a plastic takes to break down in natural environments, while recyclability testing assesses how effectively a plastic can be reprocessed for reuse. These tests are essential for ensuring that plastics align with circular economy principles and reduce environmental impact.
Key Plastic Testing Methods for Quality Control
A wide array of testing methods are employed to ensure the quality and performance of plastics. These methods help manufacturers assess a material’s ability to meet specific application requirements, identify potential weaknesses, and ensure compliance with industry standards.
1. Tensile Testing
Tensile testing is one of the most widely used methods for assessing the mechanical properties of plastics. This test evaluates a plastic’s response to being stretched, providing critical data on its tensile strength, elongation at break, and modulus of elasticity. Tensile testing is essential for determining whether a material can withstand the stresses of its intended application.
2. Impact Resistance Testing
Impact resistance testing evaluates how well a plastic can absorb energy and resist cracking or breaking when subjected to a sudden force. This is particularly important for materials used in packaging, automotive parts, and protective equipment, where impact resistance is a critical factor in product reliability.
3. Thermal Testing
Thermal testing methods such as HDT and Vicat softening point assess a plastic’s ability to maintain structural integrity at high temperatures. This ensures that plastics used in high-temperature environments, such as electronics and automotive components, do not melt or deform under operational conditions.
4. Chemical Resistance Testing
Chemical resistance testing determines how plastics react when exposed to various chemicals, including acids, bases, solvents, and oils. This test is crucial for applications like medical devices and chemical storage containers, where the plastic must resist corrosion and degradation over time.
5. Flammability Testing
For plastics used in safety-critical applications, flammability testing ensures compliance with fire safety regulations. The UL 94 flammability standard is widely used to classify plastics based on their ability to resist ignition and control the spread of flames.
The Importance of Compliance with Industry Standards
To ensure the highest levels of product quality and safety, plastics must comply with recognized industry standards. ISO, ASTM, and UL set the global benchmarks for testing and performance criteria in plastic materials. Adhering to these standards ensures consistency, safety, and reliability in plastic products, regardless of where they are manufactured or used.
ISO Standards for Plastics
The International Organization for Standardization (ISO) establishes standards for the testing and performance of plastic materials, including ISO 527 for tensile testing and ISO 11357 for thermal analysis. Compliance with ISO standards ensures that manufacturers meet international quality and safety requirements.
ASTM Standards for Plastics
The American Society for Testing and Materials (ASTM) provides comprehensive guidelines for testing plastic properties. Standards such as ASTM D638 for tensile strength and ASTM D256 for impact resistance help manufacturers ensure that their materials meet performance expectations.
Conclusion: Testing Plastics for Consistent Quality Control
Effective quality control in plastic manufacturing is impossible without thorough and reliable testing. By employing a variety of testing methods, manufacturers can ensure that their plastic products meet the necessary standards for strength, durability, safety, and sustainability. Whether used in high-performance automotive components or everyday consumer goods, testing is essential to producing plastic materials that are reliable, compliant, and capable of meeting market demands.
Investing in comprehensive plastic testing not only improves product quality but also ensures long-term business success by minimizing recalls, reducing liability, and maintaining customer trust.